Common Challenges and Solutions When Implementing Lean Manufacturing Principles
Lean manufacturing principles have become increasingly popular in various industries due to their ability to improve efficiency, reduce waste, and increase productivity. However, implementing these principles is not without its challenges. In this article, we will explore some common challenges faced when implementing lean manufacturing principles and provide solutions to overcome them.
Resistance to Change
One of the biggest challenges organizations face when implementing lean manufacturing principles is resistance to change. Employees may be hesitant or skeptical about the changes that come with lean practices. This resistance can stem from a fear of the unknown, concerns about job security, or simply a lack of understanding about the benefits of lean manufacturing.
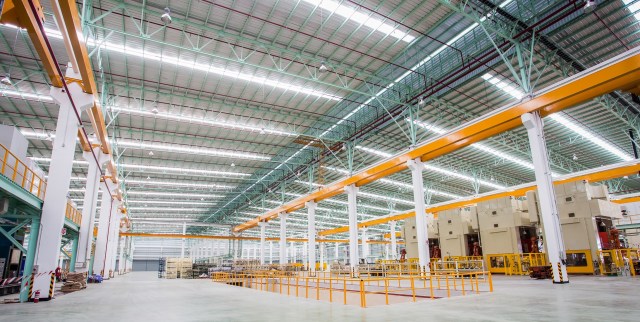
To overcome this challenge, it is crucial to provide proper training and education to employees about the principles and benefits of lean manufacturing. Clear communication is key in addressing any concerns or misconceptions employees may have. Additionally, involving employees in the decision-making process and empowering them with responsibility can help foster a sense of ownership and commitment towards adopting lean practices.
Lack of Leadership Support
Another common challenge is the lack of leadership support for lean manufacturing initiatives. Without strong buy-in from top management, it becomes difficult to drive change effectively throughout the organization. Leaders may resist change due to concerns about disruption to existing processes or a lack of understanding about how lean practices can benefit the company.
To address this challenge, it is crucial for leaders to be educated on the benefits and ROI (Return on Investment) of implementing lean manufacturing principles. Demonstrating success stories from other organizations that have successfully implemented lean practices can help gain leadership support. Additionally, aligning lean initiatives with broader organizational goals can make it easier for leaders to see how these practices contribute to overall business success.
Lack of Standardization
A lack of standardization within processes can hinder successful implementation of lean manufacturing principles. Inconsistencies in procedures or work methods can lead to inefficiencies, errors, and an inability to measure progress accurately. Without standardized processes in place, it becomes challenging to identify areas for improvement or implement continuous improvement practices effectively.
To overcome this challenge, it is essential to develop and document standard operating procedures (SOPs) for each process within the organization. SOPs provide a clear framework for employees to follow, ensuring consistency and reducing variation. Regular audits and reviews can help identify any deviations from the standard procedures and allow for necessary adjustments to be made.
Lack of Continuous Improvement Culture
A lack of a continuous improvement culture can pose challenges when implementing lean manufacturing principles. Lean practices require a mindset of constantly seeking ways to improve processes and eliminate waste. Without a culture that encourages innovation, employees may become complacent or resistant to change.
To foster a continuous improvement culture, organizations should promote open communication channels where employees feel comfortable sharing ideas and suggestions for improvement. Implementing regular feedback mechanisms such as suggestion boxes or team meetings dedicated to discussing process improvements can help encourage employee engagement. Recognizing and rewarding employees for their contributions towards lean initiatives also plays a crucial role in building a culture that embraces continuous improvement.
In conclusion, while implementing lean manufacturing principles may present challenges, they are not insurmountable. By addressing resistance to change, gaining leadership support, establishing standardization, and fostering a continuous improvement culture, organizations can successfully implement lean practices and reap the benefits of improved efficiency and productivity.
This text was generated using a large language model, and select text has been reviewed and moderated for purposes such as readability.